Improving Manufacturing with Private Wireless 5G Machine-to-machine Communications and Internet of Things (IoT)
Share
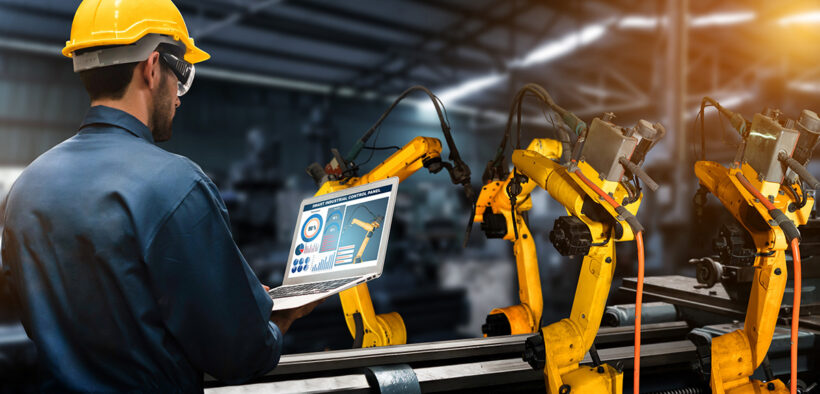
Automation is one of the most important process improvements of the modern era. It promises significant benefits for a variety of industries. One of the most clear-cut and straightforward applications of automation is in enhancing manufacturing.
Manufacturers have been looking for new and innovative ways to trim down and streamline manufacturing processes ever since Henry Ford realized that minimizing the work needed to facilitate assembly would maximize efficiency.
Networked automation built on machine-to-machine communications (M2M) and Internet of Things (IoT) technologies offers the most powerful method to date.
By effectively leveraging networked machine-to-machine communications (M2M) and IoT devices, manufacturers can automate processes to:
However, M2M and IoT technologies that can be used to automate manufacturing processes need robust, reliable, high-quality networks.
Low-latency, high-bandwidth 5G is proving to be a better option than traditional wired, Wi-Fi, and LTE networks. By deploying 5G private wireless networks, manufacturers can fully optimize the use of M2M and IoT devices to take advantage of the many benefits networked automation offers.
Automation Enhances Every Aspect of Manufacturing
The automotive industry provides a good example of the value of networked automation in the manufacturing sector. Current vehicle manufacturing facilities are highly sophisticated, software-enabled, and connected. By automating production processes, manufacturers have increased efficiency, reduced errors, and reduced the overhead associated with hiring and training personnel.
With machine-to-machine communications (M2M), IoT, and 5G wireless networks, automotive manufacturers can go one step further. They can introduce a variety of autonomous vehicles and equipment that can support and facilitate complex production processes.
Automated processes encompass tasks like delivering parts precisely when required within the facility. They also involve transporting partially completed items between different factory zones, and even moving defective products off the assembly line to minimize disruptions.
Autonomous vehicles are also sophisticated computers that require significant software and firmware to function at full effectiveness. Automating the installation, testing, and updating of this software occurs over-networked, always-on connections. This setup enables direct communication with the vehicles’ computers, making sure that complex software integration takes place early and with maximum efficiency.
While these process improvements boost production efficiency, they also enhance safety measures. Minimizing risks to personnel on the factory floor and reducing the need for their physical presence improves safety.
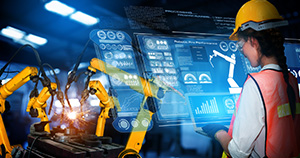
High-Quality Networks Needed
There are, however, significant challenges associated with implementing effective networked automation on a manufacturing floor.
While full automation of production can greatly enhance efficiency, it also means the entire process is more vulnerable to disruption. If the network fails at any point, even briefly, production gets delayed until network issues get resolved. And if one part of a fully automated production line is delayed, the entire chain is affected.
Similarly, autonomous vehicles and equipment on the factory floor rely on continuous connectivity to complete programmed tasks efficiently. Without those connections, they’re essentially useless. And depending on their role and the level of interaction needed with floor personnel, when these vehicles aren’t connected, they can create safety risks. Sensors can fail to alert staff in time to avoid collisions or accidents.
Finally, while automating software and firmware uploads to autonomous vehicles streamlines the ongoing maintenance and upgrade process, this is again contingent on having high-bandwidth, low-latency connections. Even brief disruptions can arrest the whole process.
Wired, LTE, and Wi-Fi Solutions Insufficient
Machine-to-machine communications (M2M) and IoT devices, essential for advancing manufacturing, produce and transmit substantial data, demanding extensive bandwidth. As a result, they require high quality, high-capacity networks. Manufacturers have tried to address the need with a combination of wired, LTE, and Wi-Fi networks. However, each of these has limitations that make them less than ideal as the foundation of a fully networked operation.
Wired connections are fast and stable but expensive to install, and once they’re installed, they’re fixed. This fixed nature makes them highly inflexible, which is a significant drawback for manufacturers that want to scale operations up or down. Manufacturers that rely on wired solutions will face expensive rip-and-replace scenarios.
Wi-Fi is a common solution for indoor network deployment and is a staple in offices and homes. But while Wi-Fi and Wi-Fi 6/6E do offer some built-in security features, they have fewer security features than LTE and 5G networks. And while network security is important in homes and offices, it’s absolutely crucial in manufacturing operations. Compromises affect operations and cause significant costs. They also expose sensitive, business-critical data to malicious actors.
Finally, LTE solutions offer both the flexibility and security that manufacturing operations need, which is why private LTE has become more common. However, while LTE offers good speed, throughput, bandwidth, and latency, it pales in comparison to the capabilities of 5G. The latest generation of wireless networking technology offers considerably greater bandwidth and vastly lower latency, two crucial elements needed for effective automation.
iBwave Enables Efficient Private Wireless 5G Deployment
Of course, networked automation, particularly in manufacturing settings, requires effective and comprehensive network design. Manufacturing floors are complex environments with numerous obstacles and sources of signal interference. Inadequately designed networks may suffer from areas of poor connectivity or even dead zones, which can significantly reduce the value of deploying automation. And the mix of indoor and outdoor environments in many manufacturing settings creates further challenges to maintaining high-quality, continuous connectivity.
Without a precise and comprehensive design, a private 5G network won’t be able to overcome the challenges of wireless network deployment in manufacturing settings. A poorly designed network will either be under-designed and fail to deliver the benefits 5G offers or overdesigned, adding unnecessary costs.
iBwave Private Networks delivers the simplest and most reliable solution for planning, designing, and deploying private, high-performance 5G networks for manufacturing settings.
Large environment modeling enables network designers to capture the full requirements of a site. 5G/HetNet densification enables designers to consider both outdoor and indoor coverage with one tool, leveraging existing design asset files without costly file migrations. Advanced and powerful features, such as the Fast Ray Tracing Prediction Engine, Prediction Calibration, Inclined Surface Modeling, and Attenuation by Frequency, ensure the network that is designed functions exactly as intended. Plus, cloud connectivity and seamless integration with iBwave Mobile Survey ensures that iBwave can meet all private network needs for any manufacturing operation, present and future, ensuring the network can scale with the operation as needed.
To learn more about design considerations in private networks for manufacturing, watch our on-demand webinar: https://bit.ly/3X5zXK2
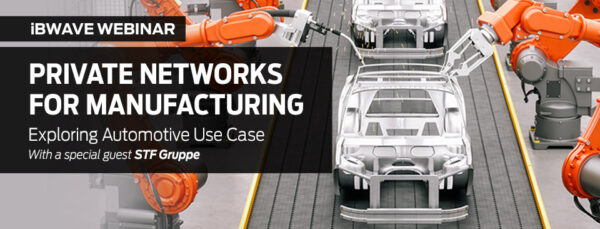